What are the Challenges in PET Bottle Recycling
PET, or polyethylene terephthalate, is a popular plastic used for packaging due to its strength, clarity, and recyclability. While recycled PET (rPET) is vital in reducing plastic waste and conserving resources, the recycling process faces multiple challenges that affect efficiency and economic viability. This post will explore some of the biggest hurdles in PET bottle recycling and potential solutions for a more sustainable future.
The Problem with Colored Bottles
Green bottles, traditionally used for their shelf appeal, particularly for lemon-lime drinks, pose a significant challenge. The green dye complicates the recycling process and contaminates recycling streams, requiring extra effort for sorting and processing. The higher percentage of green bottles in India, around 10 percent, exacerbates the issue.
Similarly, other colored PET bottles, used by brands for marketing and branding purposes, also present problems. The additives used in these bottles are often difficult to remove during recycling. Separating colored bottles from clear ones necessitates complex machinery. Moreover, the lower selling price for colored bottles, compared to clear ones, discourages collectors, further hindering their recycling. Colored bottles also result in lower quality rPET.
Several countries, including the USA, EU, and UK, have started phasing out green bottles due to these challenges. Major brands like Coca-Cola and PepsiCo are shifting to clear bottles, recognizing their improved recyclability and higher value in the recycling market. South Korea has also replaced many colored bottles with colorless ones following the implementation of its revised Act on the Promotion of Saving and Recycling of Resources in 2019.
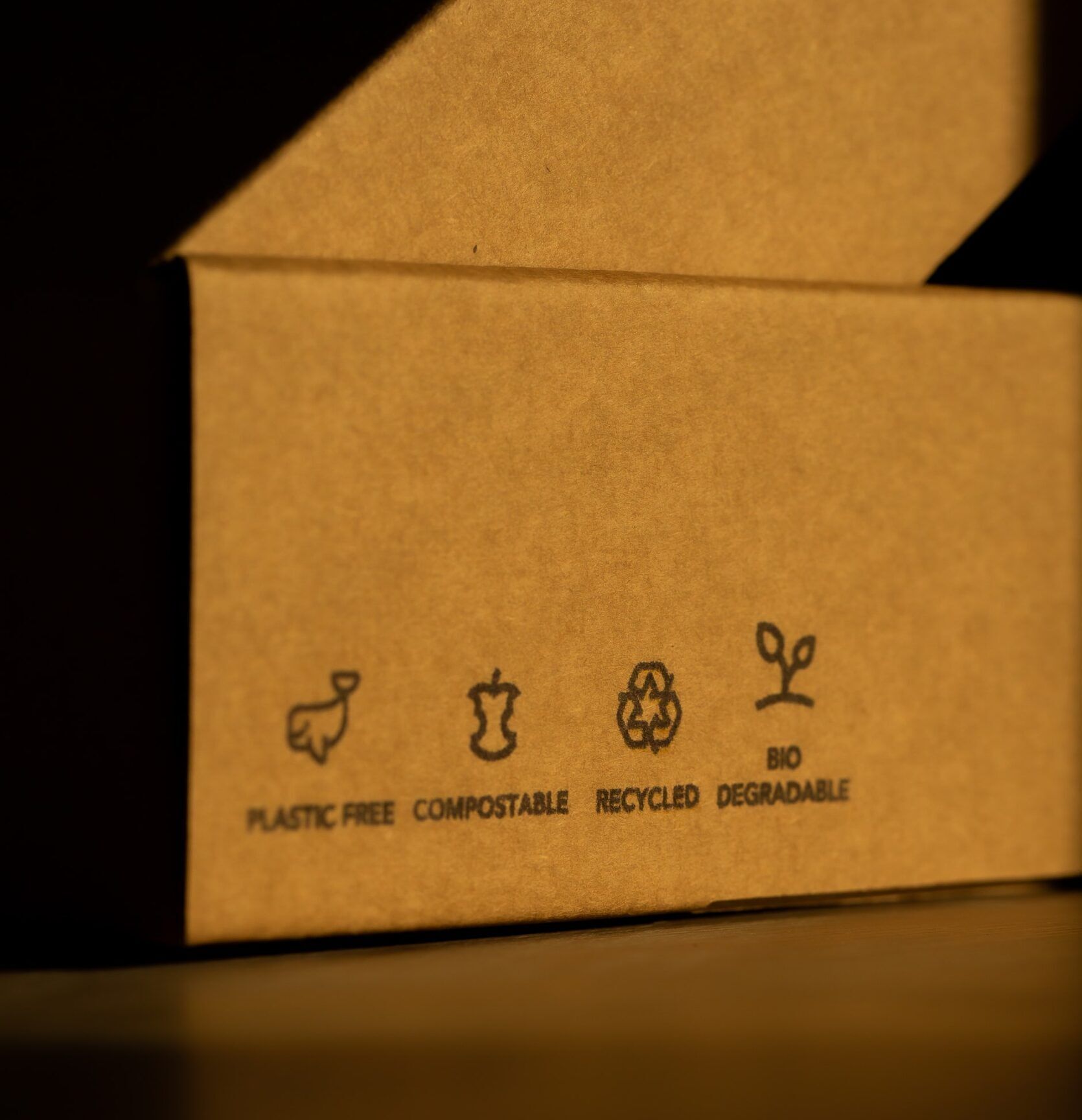
South Korea: A Success Story:
South Korea has implemented new packaging material and labelling requirements for cosmetic products, reflecting the country's commitment to environmental sustainability and consumer awareness.
Since the end of 2019, South Korea has banned the use of PVC materials and coloured PET bottles in cosmetic packaging. Companies are now required to evaluate and grade the recyclability of their packaging materials.
To address concerns about products graded as "difficult to recycle," the Korean Cosmetic Association (KCA) and Korea Packaging Recycling Cooperative (KPRC) introduced the Reverse Recycling Scheme of Cosmetic Containers in 2020. This initiative allows companies to collect used containers from consumers, potentially exempting them from the "difficult to recycle" label.
These new requirements pose challenges for cosmetic companies, particularly those using colored containers or complex materials to protect product efficacy. However, they also present opportunities for brands to demonstrate environmental responsibility and appeal to increasingly eco-conscious Korean consumers.
Read more in this
link:
Packaging Choices That Complicate Recycling
Full sleeve bottles, favored for their enhanced visibility and product differentiation, create difficulties with label removal during recycling. The different melting points of label materials, such as PVC and PETG, can contaminate the PET recycling stream, impacting the quality and market value of rPET flakes.
PVC labels, while cost-effective and versatile, pose significant challenges due to their similar density to PET. This leads to contamination in float-sink separation tanks. Additionally, the chlorine content in PVC can release harmful chemicals during recycling, further contaminating the process and posing environmental and safety risks. Taiwan's recent ban on PVC packaging highlights the growing concern over this material.
Material Components That Cause Issues
Aluminum caps and rings, though lightweight and offering an effective seal, necessitate expensive eddy current machinery for separation from PET bottles. Their small size and flat shape often cause them to slip through sorting screens or get stuck in machinery, leading to damage.
Silicone/rubber seals inside caps, crucial for maintaining product freshness and preventing leakage, present major difficulties in recycling. Their incompatibility with PET melting points contaminates the recycling stream, affecting the quality and value of rPET. Traditional methods like flake sorters are ineffective in removing these seals due to their jumping properties.
Bottle Types That Pose Problems
Low melt PET bottles, used for packaging products requiring hot-filling, have a higher melting point than standard PET bottles, leading to uneven melting and contamination during recycling. This affects the quality of rPET and can cause processing inefficiencies and equipment damage.
Lightweight PET bottles, while offering cost and environmental benefits, are difficult to separate effectively using standard sorting technologies. Their thin walls also tend to degrade during recycling, resulting in lower-quality rPET.
Small PET bottles, popular for their convenience, are prone to improper disposal and can be missed during sorting due to their size. Their smaller volume necessitates collecting and processing more bottles to achieve the same rPET output as larger bottles, increasing costs.
The type and quality of glue used for attaching labels to PET bottles can also impact recycling. Strong adhesives make it challenging to remove labels cleanly, contaminating the recycling stream and affecting rPET quality. Certain adhesives can even cause issues in recycling machinery, leading to increased maintenance and downtime.
Potential Solutions
The sources highlight various potential solutions to these challenges, emphasizing the need for collaboration between brands, recyclers, and policymakers:
- Phasing out problematic materials: Transitioning from colored PET bottles to clear ones, replacing PVC labels with alternatives like BOPP, and substituting aluminum caps with HDPE caps are crucial steps.
- Improving sorting technologies: Investing in advanced sorting systems that can effectively separate different materials, including lightweight and small PET bottles, is essential.
- Developing compatible materials: Encouraging the use of recyclable materials for bottle cap seals and labels, such as TPEs and water-soluble adhesives, can facilitate cleaner recycling.
- Redesigning packaging: Collaborating on bottle designs that prioritize recyclability, such as incorporating detachable components or standardized shapes, can enhance the efficiency of recycling processes.
- Promoting public awareness: Educating consumers on proper disposal and recycling practices, particularly for lightweight and small bottles, can minimize contamination at the source.
Conclusion
Addressing the challenges in PET bottle recycling requires a multifaceted approach involving innovations in materials, design, and technology. By working together, stakeholders can enhance PET bottle recyclability, support a circular economy, and create a more sustainable future for the packaging industry.
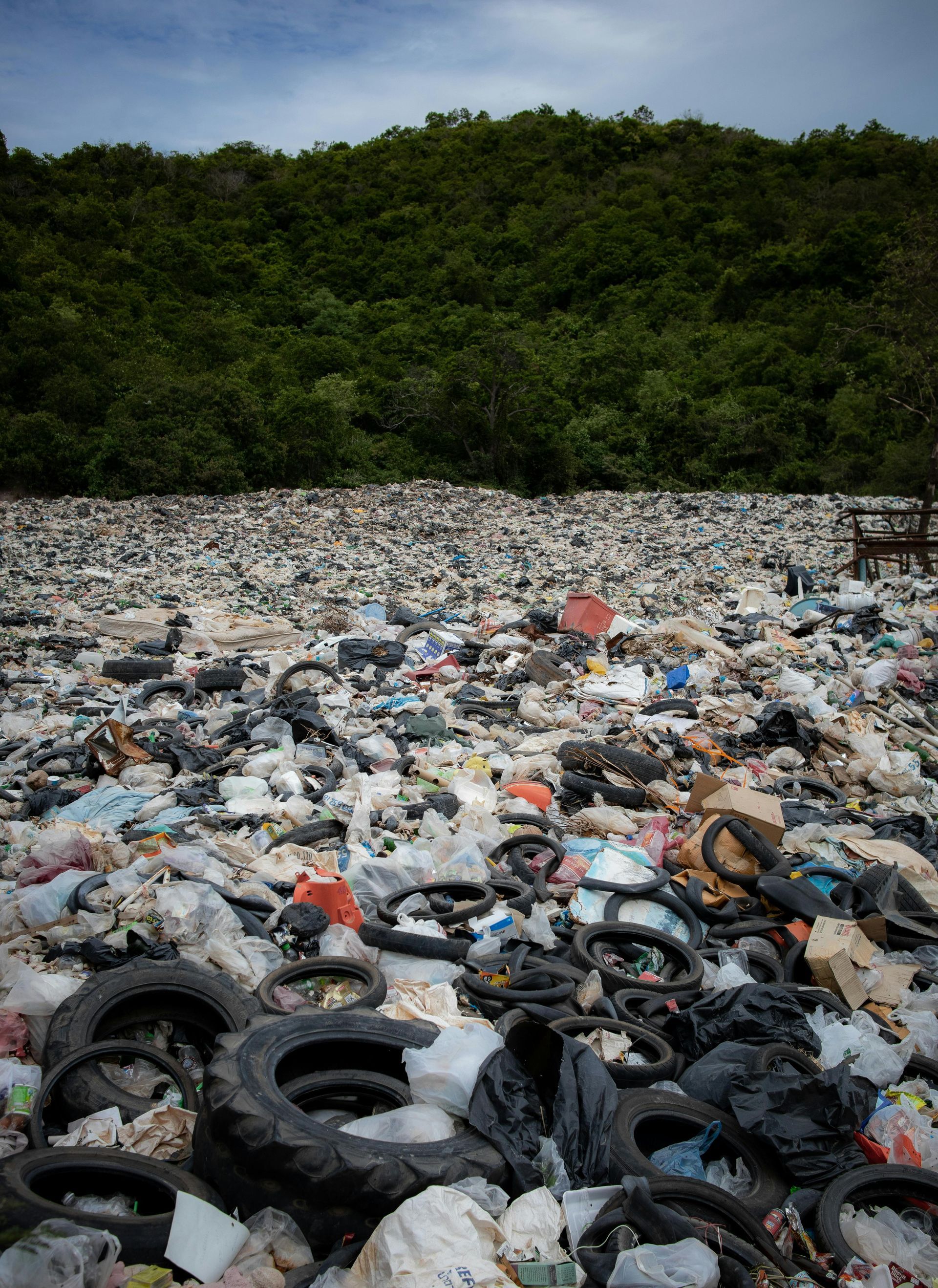
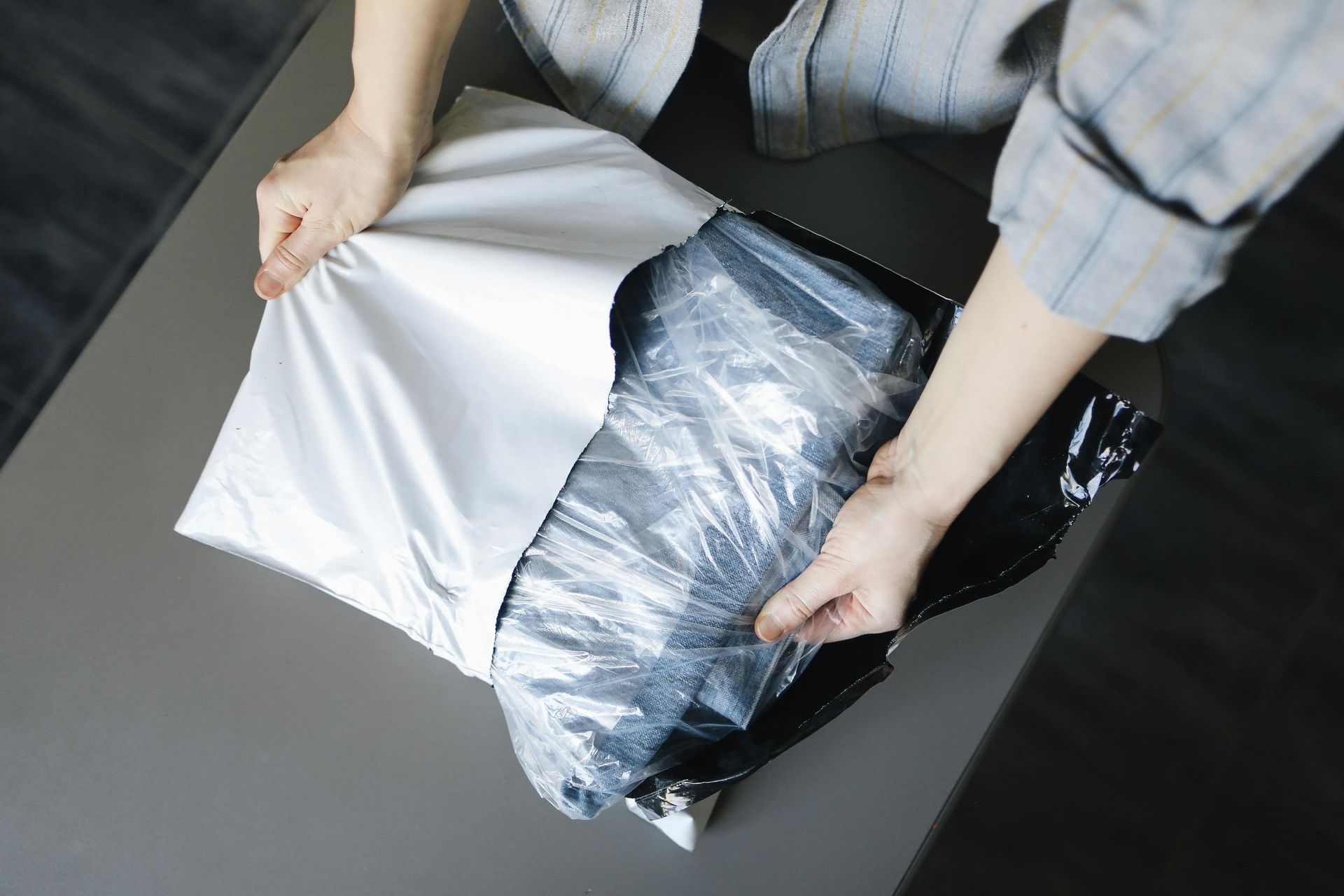
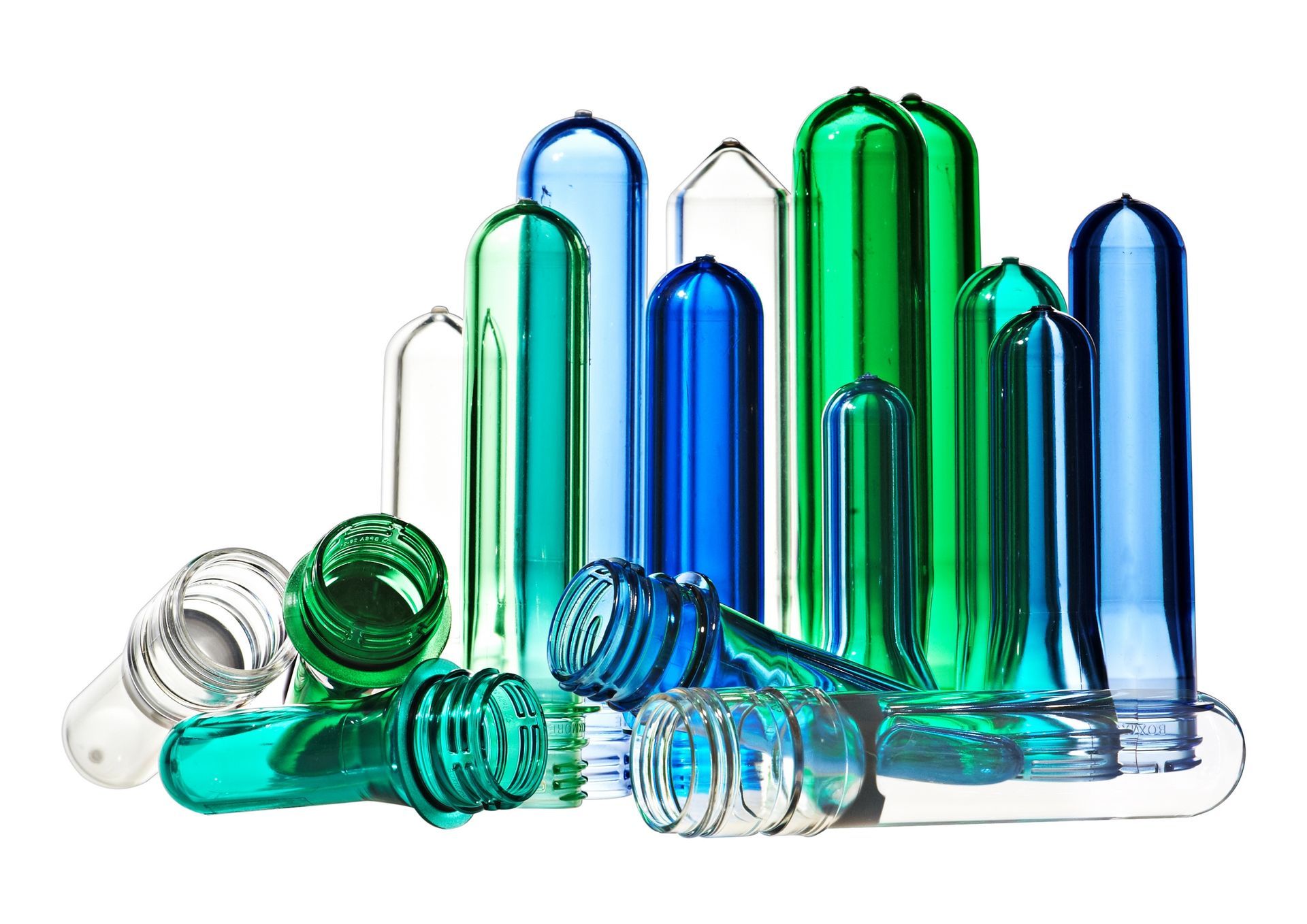